Our Steam Boiler Treatment Program is designed to provide the optimum scale and corrosion protection to help prolonging the life of the boiler system and improving the boiler efficiency to reduce the fuel costs and operational downtime.
The cost of your water management program typically represents approximately 2–4% of the overall operating costs to run your steam system. Just 1/16” of scale can increase fuel consumption by 12%. That’s why it’s important to invest in a well-executed program that delivers results over the asset life cycle.
Our Boiler Treatment programs are tailored to prevent corrosion, prevent scale build up and protect your return line.
CORROSION INHIBITORS
The addition of oxygen to a system with water and heat will initiate corrosion. Heat, found in the feed water system, is a driving force for corrosion. The ability for oxygen to attack forming a pit on metal, increases by a factor of two for every 10ºC (18ºF) rise in temperature. Oxygen can be 512 times as aggressive at 212º than it was at 50ºF. Mechanical deaeration, can remove most, but not all of the oxygen from the water. An oxygen scavenger is used to eliminate the remaining oxygen. Properly applied, oxygen scavengers will prevent oxygen pitting and extend the life of your boiler.
Every boiler setup is a little different based on feed water, size, operating parameters and boiler usage. We offer several different corrosion inhibitors to provide the optimal coverage of your boiler based on your situation.
SCALE INHIBITORS
Boiler scale is caused by impurities being precipitated out of the water directly on heat transfer surfaces or by suspended matter in water settling out on the metal and becoming hard and adherent. Evaporation in a boiler causes impurities to concentrate. This interferes with heat transfers and may cause hot spots, leading to local overheating.
Common feed water contaminants that can form boiler deposits include calcium, magnesium, iron, aluminum, and silica. Scale is formed by salts that have limited solubility but are not totally insoluble in boiler water. These salts reach the deposit site in a soluble form and precipitate onto the tubes of the boiler.
Even a small increase in scale can drastically increase the operating costs of a boiler as you can see from the chart below. Scale can also produce damage to the boiler if hot spots occur, cause unscheduled down time and increase cleaning expense.
Our Chemical Treatment Program takes into account the feed water quality, internal treatment products to the boiler feedwater quality to prevent scale and excessive sludge accumulation. Utilizing the most advanced polymer technology available provides optimum fuel efficiency and performance
RETURN LINE TREATMENT
The primary causes of corrosion are carbonic acid attack and oxygen pitting in return line systems. This corrosion can cause unexpected system shutdowns, affecting production timelines and costly repairs. Corroded systems are also less efficient, risking leaks and potentially cause damage to the boiler as corrosion by products are carried back into the feedwater.
The condensate return line treatments react quickly to neutralize condensed steam carbonic acid with amines to neutralize the return line and buffer the pH level to prevent corrosion. There are many types of condensate treatments, but the most common are amines. We carry several different return line treatments to offer full protection no matter weather it is a short, medium or long return line system.
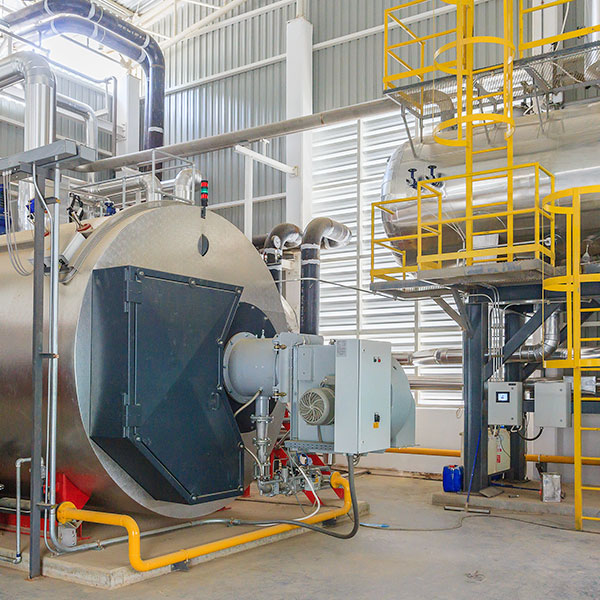
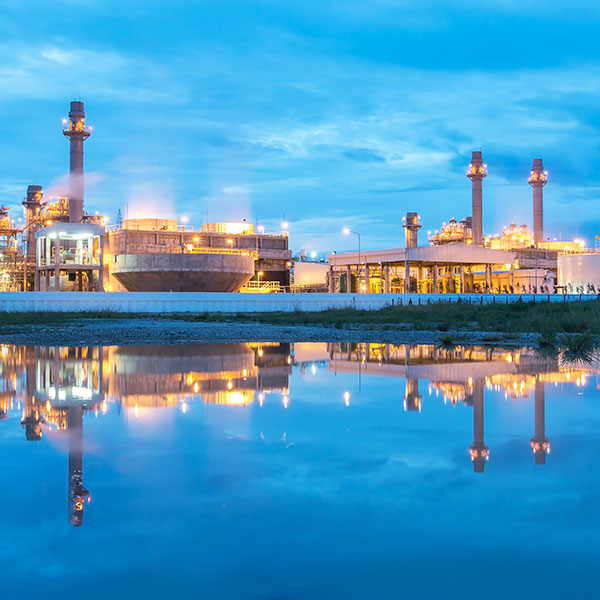